Service Support
Maintenance
To ensure continuing process capability a scheduled programme of servicing / maintenance is operational within Weld-A-Rail.
Scheduled servicing / maintenance of equipment, having a direct effect on product quality, is undertaken by Weld-A-Rail’s sister company Powerflo (Midlands).
Powerflo (Midlands) operate at the leading edge of technology in respect of equipment maintenance / servicing, repair and calibration.
Digital systems have been developed for all associated activities including gas equipment and straight edge calibration and are fully operational.
All servicing is controlled through a unique servicing database “Service Desk”.
Service Support
Weld-A-Rail provide service support for a period of up to 1 year, with a response
time of 8-24 hours with no geographical limits.
The company operates a fleet of 30 fully equipped welding vehicles.
Weld-A-Rail operatives will undertake a visual inspection of all completed welds in accordance with NR/L2/TRK/0032 Joining of Rails by Alumino Thermic Welding for:
- Gross Porosity in the Weld Collar
- Porosity or Surface Cavities in the weld collar that penetrate in to the Rail Section
- Collar Distortion
- Evidence of incorrect preheating conditions, e.g. smooth collar surface
- Incomplete collar formation
- Black holes
- Porosity or cracks on the contour of the head of weld.
In addition, the relevant competency and experience exists within Weld-A-Rail should it be required and appropriate, to undertake a complete inspection of Alumino Thermic welds cast.
A record WQF3057 Weld Installation Sheet is maintained and completed in accordance with WQF3071 Weld Installation Sheet Instructions for all completed welds giving details as appropriate of:
- Customer
- Date of weld
- Route
- Location
- Mileage
- Line
- Rail
- Welding process
- Rail profile(s)
- Rail grade(s)
- Portion and batch number
- Ignition to tap time
- Weld type (standard, stepped, composite, etc)
- Welder’s name
- Welder’s stamp number
- Welder report reference (in the case of a defective or suspect weld report)
- Company name.
Copies of the Weld Installation Sheet are forwarded to the customer within five working days of the weld being cast.
Records are maintained by Weld-A-Rail of all completed welds to facilitate complete traceability. Failed welds are identified and analyzed with corrective and preventative action taken to ensure the best quality can be achieved and the elimination of future failures.Subsequent to the work being completed the customer will undertake an independent inspection of the welds completed by the company and advise of any defects identified.
On receipt of a Customer Rejection Report Weld-A-Rail will undertake any
necessary corrective action in accordance with WQP102 Control of Corrective and Preventative Action.
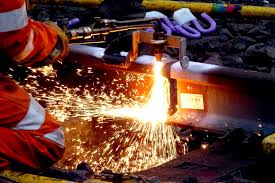